How Thoughtful Design and Metal Fabrication Software Help Boost Your Bottom Line
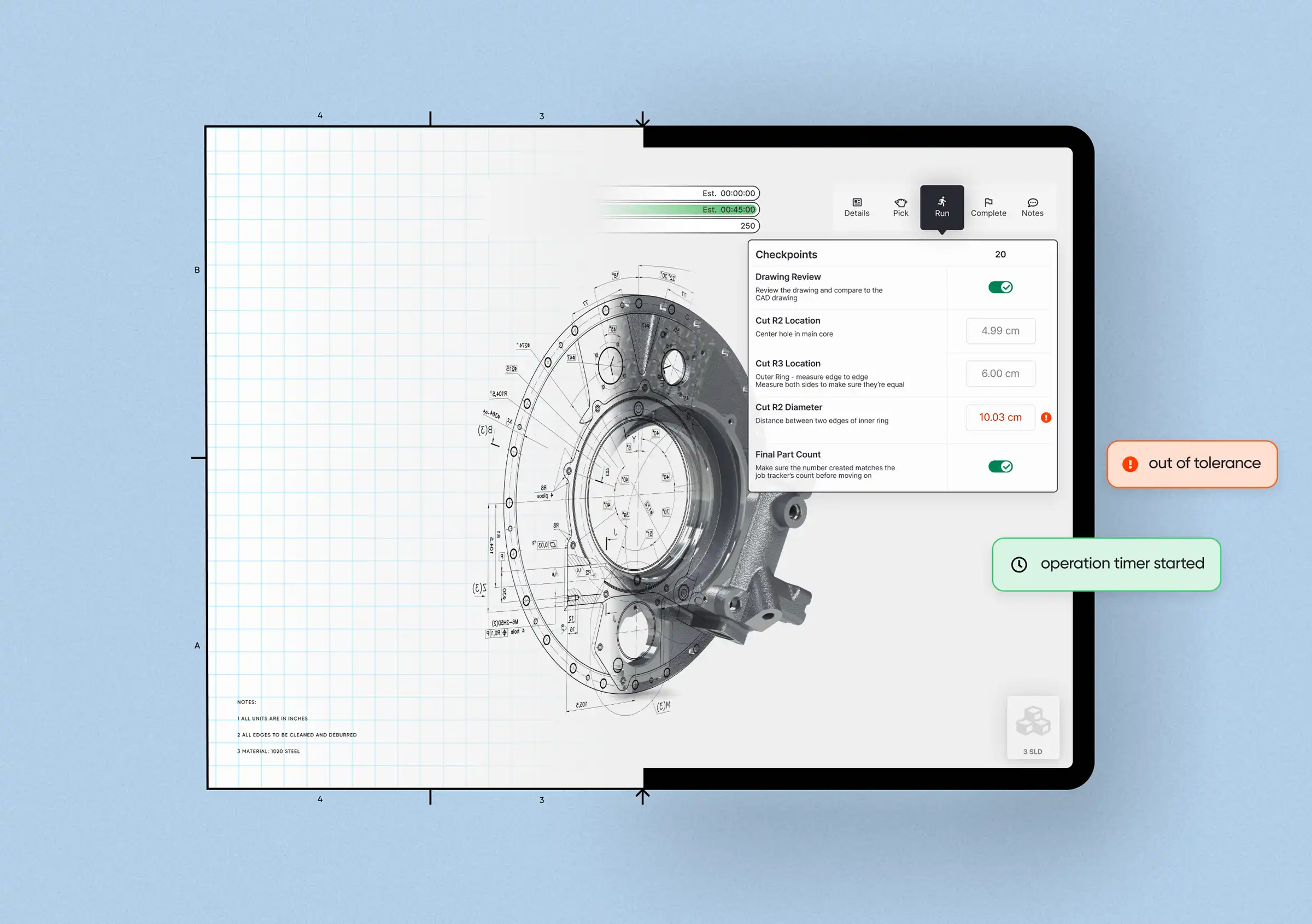
As we talk with sheet metal fabrication businesses across the country, a common theme in their day-to-day life is balancing their costs while keeping quality high. This includes finding the right equilibrium by factoring in their team, customer demands, the details of the jobs they’re quoting, inventory and purchasing, the work on the shop floor, quality checkpoints, and more. While there’s no one-size-fits-all solution to this complexity, there are some best practices. In this article, we'll explore some strategies and how to align technology like ERP, MRP, and MES to elevate how sheet metal fabrication work gets done right, and profitably.
Design for Manufacturing (DFM) Approach
Effective cost reduction in sheet metal fabrication starts with thoughtful design. Embracing Design for Manufacturing (DFM) principles ensures a smooth transition from design to production, resulting in an optimized process with minimal revisions and delays.
Key DFM considerations include:
- Simplifying part geometries. By reducing design complexity, you'll eliminate the need for specialized tooling and labor-intensive processes, effectively lowering production costs without sacrificing creativity. Tools like Solidworks can help you simplify parts and assemblies, reducing unnecessary complexity.
- Fine-tuning bend radii. Selecting suitable bend radii for each material and thickness mitigates the risk of material issues, leading to a cost-effective and durable product.
- Reducing welds. Decreasing the number of welds in a design not only cuts labor costs but also creates a more efficient and reliable product.
- Setting and measuring practical tolerances. Specifying appropriate tolerances prevents over-engineering and reduces production costs without compromising quality or performance. A metal fabrication software like Fulcrum helps you communicate tolerances by including them as a part of an operations instruction.
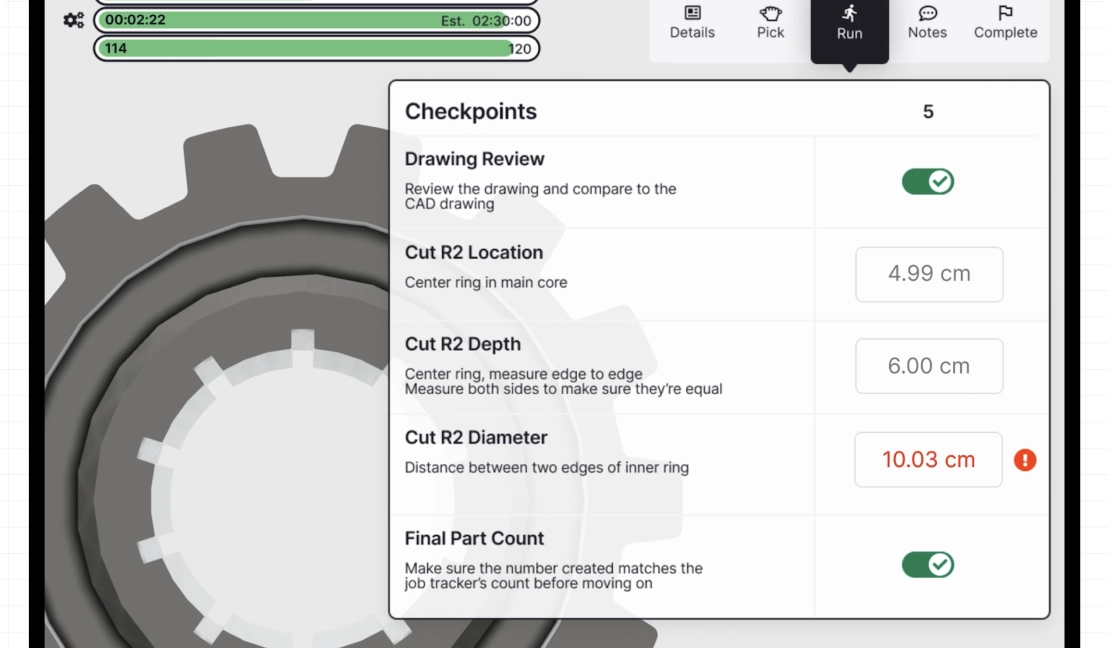
The Art of Material Optimization
Efficient raw material usage is the backbone of cost-effective sheet metal fabrication. By maximizing material utilization and minimizing waste, you will achieve a more cost-effective production process. Consider these material optimization strategies:
Nest parts strategically. Arranging parts on a sheet of metal to minimize scrap and optimize available material is a skill worth mastering. Nesting software like Sigmanest and Fusion 360’s nesting extension can help you to use the most of every material automatically, and a metal fabrication ERP software like Fulcrum that can integrate with nesting software and allow you to group jobs into work orders can help you track inventory.
Design and purchase smarter. Opting for standard material sizes will reduce waste, lead times, and costs associated with custom materials. Additionally, if engineers are aware of standard sheet metal sizes, they are more likely to design parts with those sizes in mind. By assessing your material usage over time, you can see what material sizes you use the most often and focus on purchasing those materials. Purchasing planning software can help you group demand by material, compare vendor prices to find the best price, and see automated purchasing recommendations that make sure you’re not paying extra for rushed shipping fees.
Embracing Automation and Technology: Front Office and Shop Floor
Adopting modern cloud technology and automation enhances efficiency, precision, and consistency in sheet metal fabrication. Automation happens on the shop floor with robotic welding, automated cutting, and CNC bending machines that can mitigate human error and boost production speed. Planning in the front office with automation can see gains from modern technology as well. An advanced sheet metal fabrication software helps further refine the fabrication process, reduce waste, and use algorithms to schedule smarter.
Adapting Lean Manufacturing to Fabrication
Many sheet metal fabrication leaders adopt continuous process improvement and lean manufacturing principles, modifying structure to be the right level of rigor while not getting bogged down. By evaluating and refining each step of the fabrication process, shops can eliminate bottlenecks and waste.
Lean manufacturing strategies to consider:
- Value stream mapping. Value stream mapping helps you identify areas of waste and inefficiency within the production process, enabling targeted improvements.
- Root cause analysis. Diligently identify the root causes of production issues and implement corrective actions to enhance overall efficiency. Digital production tracking software helps record scrap reasons and NCRs so that you have accurate data to work with. With more raw data, you can visualize root causes of nonconformance so you know exactly where you need to make an adjustment.
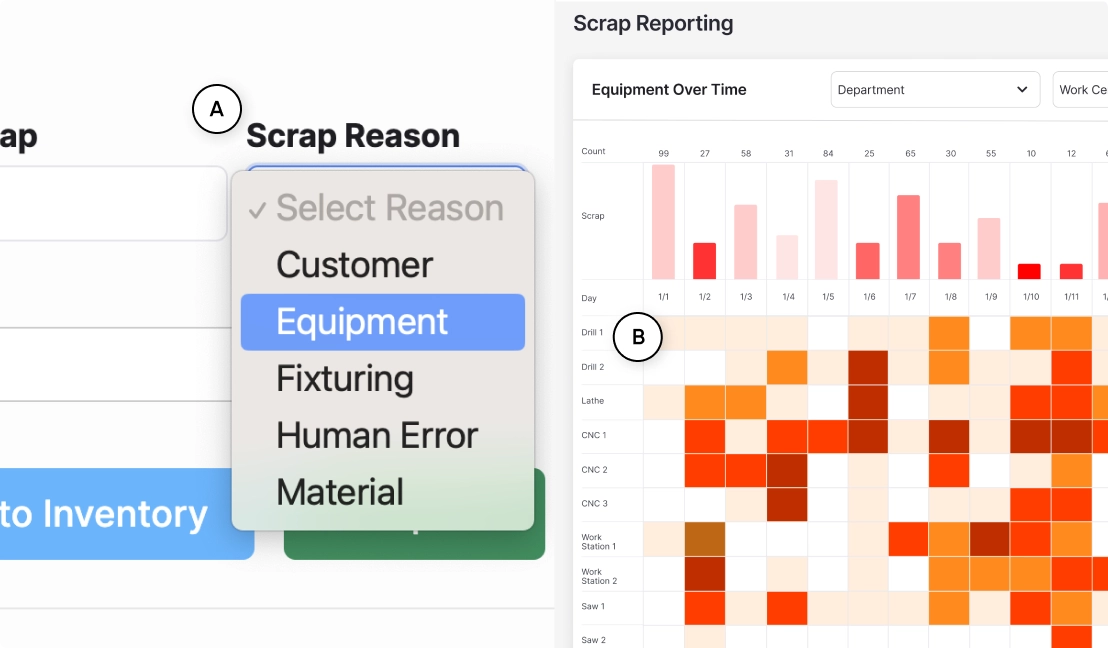
- Preventative maintenance. Regular equipment maintenance reduces downtime, prolongs equipment lifespan, and ensures optimal performance. Additionally, a dynamic scheduling tool can assist in automatically rescheduling around machines with downtime, rerouting to machines with the same functionality.
- Employee training and communication. Invest in employee training and skill development to maintain a highly skilled workforce capable of handling complex fabrication tasks efficiently. Additionally, providing comprehensive, clear instructions on every operation and a streamlined way to have frictionless communication can help spread information faster.
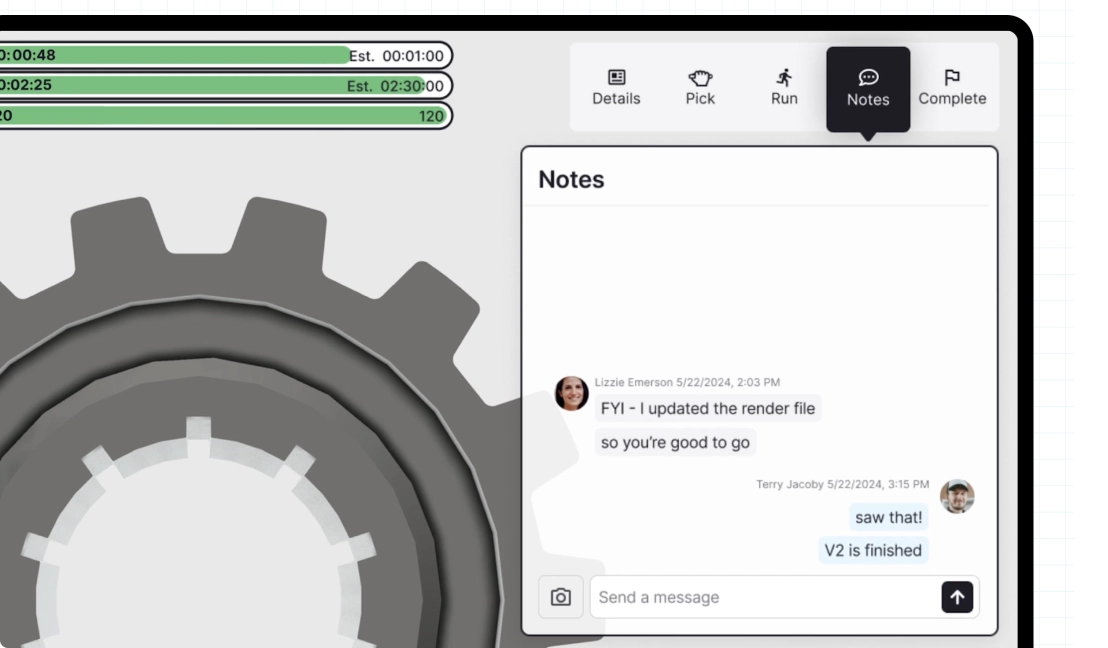
Building Strategic Vendor Relationships and Supply Chain Management
Establishing strong relationships with material suppliers and subcontractors can have a significant impact on overall project costs.
Having a system in place to compare the quality and prices of your vendors can help you understand where to invest your time in developing relationships with suppliers. A tangible way to evaluate vendors is to assign quality scores, which are calculated by on-time percentages and the rate of issues to help you choose the best partner for your business.
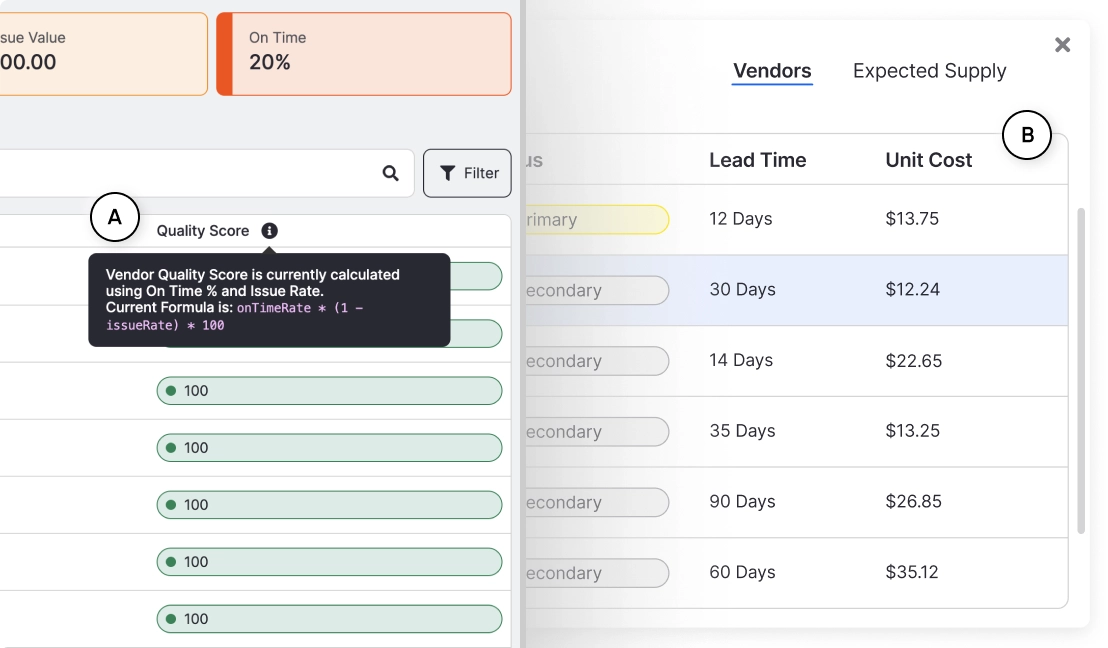
Effective supply chain management can help reduce lead times and minimize inventory costs by optimizing order quantities and scheduling deliveries in accordance with production needs. Rather than doing this manually, metal fabrication inventory software like Fulcrum provides customers with automated purchasing recommendations for materials and subcomponents based on demand.
Quality Control and Inspection: A Testament to Perfection
Implementing a robust quality control system is essential for minimizing rework, scrap, and production delays. A comprehensive quality control program in place can detect and address issues early in the production process, reducing costs associated with defects and ensuring customer satisfaction. Applying data-driven quality control methods, such as statistical process control (SPC) and non-destructive testing (NDT), helps identify trends and prevent issues before they escalate. Regular calibration of measurement and inspection equipment, as well as employee communication about quality control techniques, further enhances the effectiveness of the quality control system.
In Fulcrum, statistical process control signals operators when deviations from tolerances start to occur, enabling timely adjustments and waste reduction. Thorough pre- and post-checks guarantee that no detail goes unnoticed, helping you prevent problems before they start.
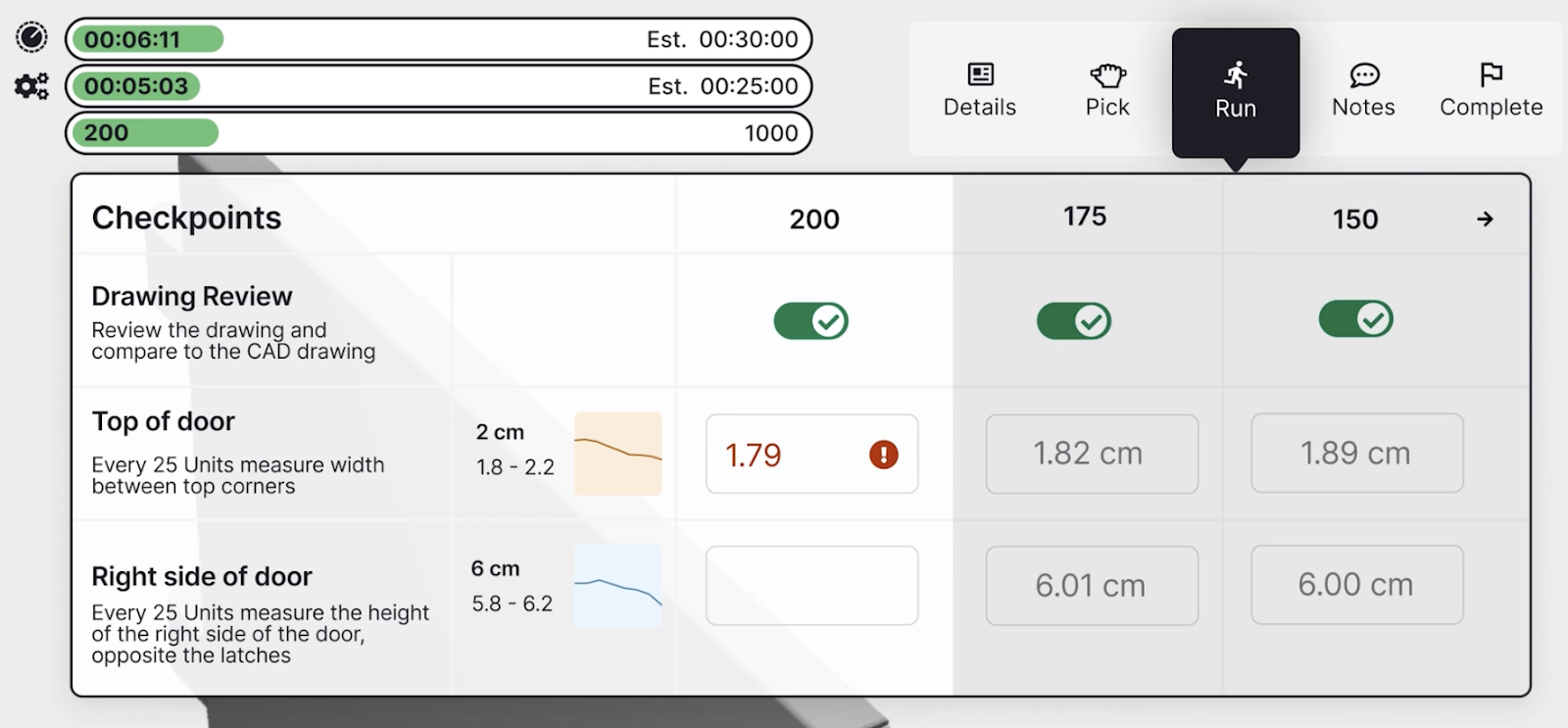
Energy Efficiency and Sustainability
Embracing energy-efficient practices and sustainable processes in sheet metal fabrication can lead to significant cost savings. By adopting energy-saving technologies, such as energy-efficient lighting and machinery, you can reduce energy consumption and lower utility bills. Additionally, recycling scrap materials and reducing waste contribute to a more environmentally friendly operation and can result in cost savings through reduced material disposal expenses and potential revenue from selling recyclable materials.
Process Documentation and Communication
Detailed documentation of fabrication processes facilitates knowledge sharing, standardization, and continuous improvement. By maintaining clear and accessible records of each step in the production process, you can ensure that employees have the necessary information to perform their tasks accurately and efficiently.
Communication is an important part of continual improvement. By enabling live chat and digital notes for operators and production managers, Fulcrum puts the right information in the right place at the right time. One of the best ways to manage the data is to increase the accountability on both ends: the shop floor holds production supervisors accountable for poor instructions or missing information on the job and vice versa. By building a culture of good data, you can decrease the need for complexity and take advantage of clear insights.
—
In the dynamic world of sheet metal fabrication, the path to success is paved with creativity, innovation, and an unwavering commitment to excellence. By exploring and incorporating new technology, you can elevate your business to new heights, delivering exceptional quality without compromising profitability.
This article was written with the help of Ai.