Next Generation BOM: The Future of the Bill of Materials
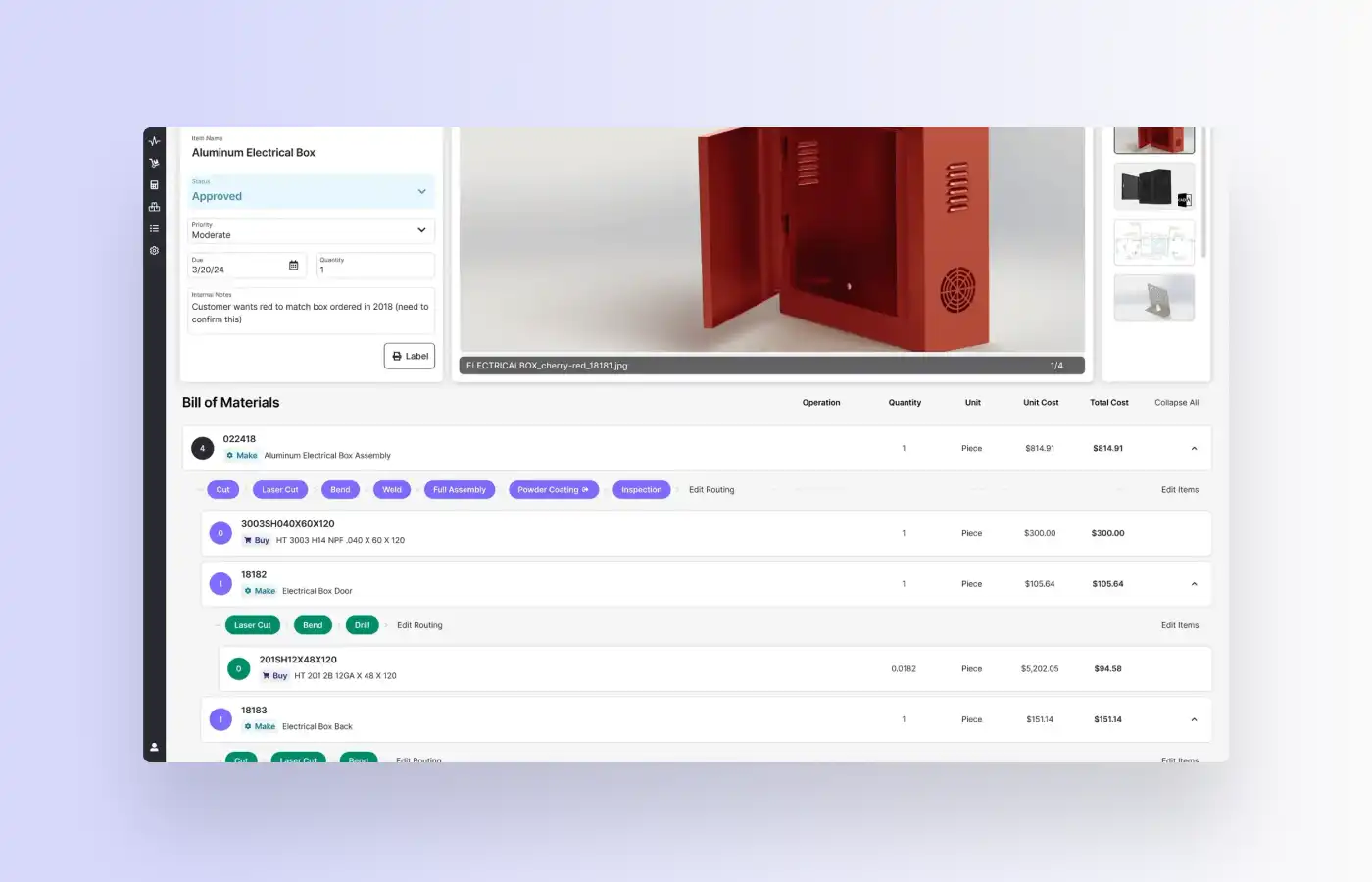
Before we leap to what the future looks like, let’s start with the basics:
What is a Bill of Materials (BOM)?
The bill of materials is an essential part of manufacturing. It details exactly what goes into the final good being produced for the next stage of production or for sale to the customer. The bill of materials, BOM, lets the shop know which materials need to be removed from inventory and in which quantities.
A BOM can take almost any form, however a typical one will have a final good that is being produced from a collection of raw materials and already fabricated materials. These previously fabricated materials are known as subassemblies or intermediate goods. A BOM with one parent item (the final good being produced) and raw material components is known as a single-level BOM. Raw materials are transformed into the final product and do not require additional fabrication before they are ready to be assembled. A multi-level BOM contains a mixture of raw materials and finished subassemblies. These subassemblies must be fabricated before the final assembly can begin, introducing dependency to the workflow. In some cases, the subassemblies are built to inventory stock, allowing them to be picked and placed into the fabrication process immediately. Otherwise, the shop floor must accommodate for the fabrication of subassemblies so that the final product is delivered on time.
What role does software play in the future of Bill of Materials?
Before Enterprise Resource Planning (ERP) or Manufacturing Resource Planning (MRP) systems were commonplace, the BOM would be written or typed out in a format that is logical to those creating the BOM and those fabricating the materials. Now, modern systems apply digital record-keeping for easier information retrieval as well as automated workflows to make production planning, operations, purchasing, and finances more streamlined.
Multi-level Bill of Materials structure: organizing for success
The parent item will take priority, with child items listed below, along with the quantities required. A multi-level BOM is more complicated in this respect. The final product will continue to take priority over the subassemblies, but those subassemblies will have to list their child items in a meaningful way so that the shop can tell what components go into the subassemblies and which are necessary for the fabrication of the final good. Software can be very helpful in organizing these materials into a format that makes sense to anybody viewing the record. The top level of the BOM will read as the final product, including the quantity being made. Subassemblies and raw materials will be listed as parallel items under the parent to indicate that these items are children of the parent item. Subassemblies will also have their own parent/child breakdown.
Bill of Material Software’s role is to create a list structure that hides components of the subassemblies until they need to be referenced. The result is a clean, multi-level BOM structure that can be observed and understood by anyone familiar with the shop’s manufacturing process.
For a first-hand view of a modern BOM in action, schedule a live demo or explore Fulcrum’s Drag-and-Drop BOM & Routing Software.
// This article was updated 4/04/23.