How a Metals ERP Can Boost Your Metal Fabrication Business
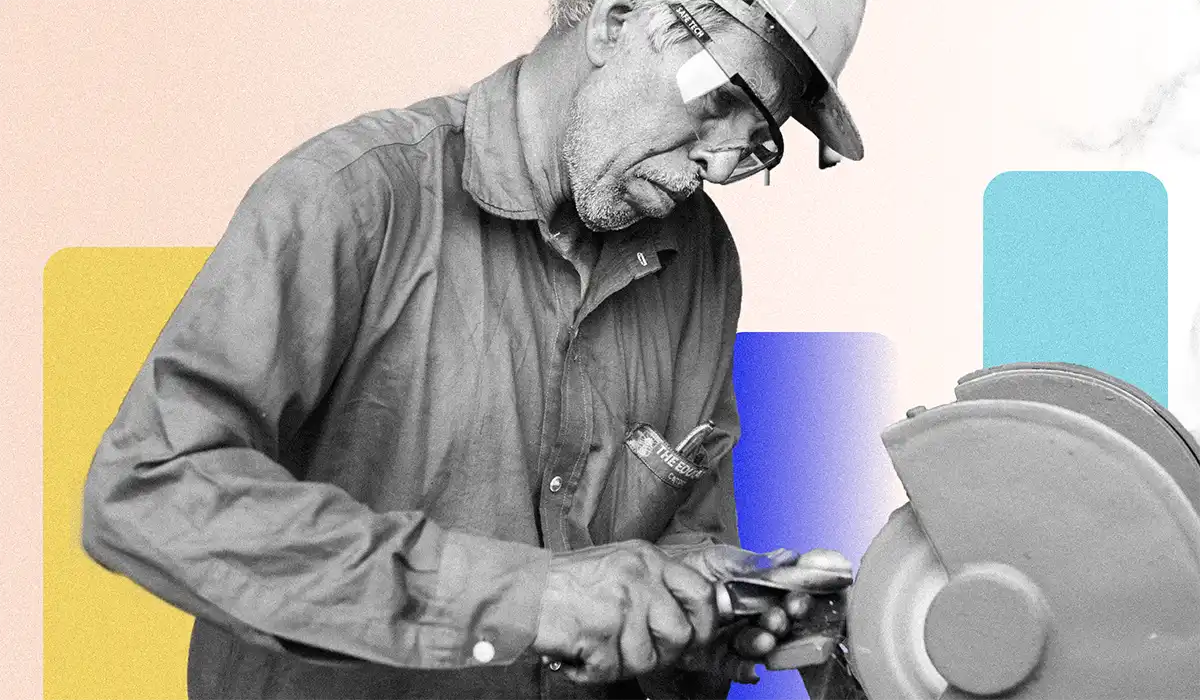
Metal fabrication is a complex and competitive industry requiring high efficiency, quality, and customer service. As a metal fabricator, you must manage your inventory, production, sales, and finances effectively to stay ahead of the competition. Still, many metal fabrication businesses rely on outdated or generic software systems that cannot handle the modern challenges and requirements of the industry. These systems were architected in the 1980s with little change since and need more functionality, flexibility, and integration to optimize operations and grow your business in the modern era.
That's why you need a modern metals ERP (enterprise resource planning) solution designed for your industry and tailored to your needs. A metals ERP solution can help you streamline your processes, improve your performance, and increase your profitability.
What is a metals ERP?
A metals ERP is a software system that integrates all aspects of your metal fabrication production into one platform. They cover everything from quoting and estimating to inventory management, production scheduling, quality control, shipping, and invoicing — while integrating with other business-critical software for accounting, CRM, and more.
A metals ERP solution can help you:
- Reduce costs by minimizing waste, scrap, and errors
- Increase efficiency by automating tasks and workflows
- Enhance quality by tracking specifications and certifications
- Improve customer service by providing accurate and timely information
- Gain insight by generating live reports and dashboards
What are the benefits of a metals ERP?
By implementing a metals ERP solution, you can expect to see significant benefits for your business, such as:
- Increased productivity: The use of Metals ERP software can enhance productivity by optimizing the utilization of materials, machines, and labor, while also improving job planning and execution efficiency, ultimately leading to reduced downtime and delays.
- Improved accuracy: By eliminating the need for manual data entry and duplication, a metals ERP system can effectively prevent errors and inconsistencies. Furthermore, it can aid in meeting industry standards such as ISO9100 and fulfilling customer requirements, thereby reducing rework and returns.
- Enhanced visibility: Metals ERP solutions can help you gain real-time visibility into your inventory levels, production status, customer orders, and financial performance. It can also help you monitor key performance indicators (KPIs) and identify areas for improvement.
- Greater flexibility: With the ability to automatically aggregate data, a metals ERP solution can assist in adapting to evolving market conditions and customer demands. Additionally, it can facilitate tailoring products and services to meet specific preferences and requirements.
How does a metals ERP work?
A metals ERP solution works by connecting all the data sources in your business into one central database that different modules or applications can access and aggregate. These modules or applications perform various functions that support your core business processes.
Below are some of the critical modules or applications that a metals ERP solution offers.
Bill of Materials (BOM) & Routing. This module allows you to create, maintain, and control your BOM and Routing and get live cost calculations. You can import CAD file details or use a BOM template to import your items, then clone them for future quotes, sales orders, or things you're making to stock. You can also define routing steps, operations, work centers, labor rates, overhead rates, and set-up times for each product or process.

Quoting & Production Estimating lets you create accurate and professional quotes and estimates for your customers in minutes. You can use predefined templates, import BOMs and routings, apply markups and discounts, calculate labor and material costs, add attachments and notes, and send quotes via email or PDF. You can also track quote status, follow-up actions, revision history, and conversion rates.
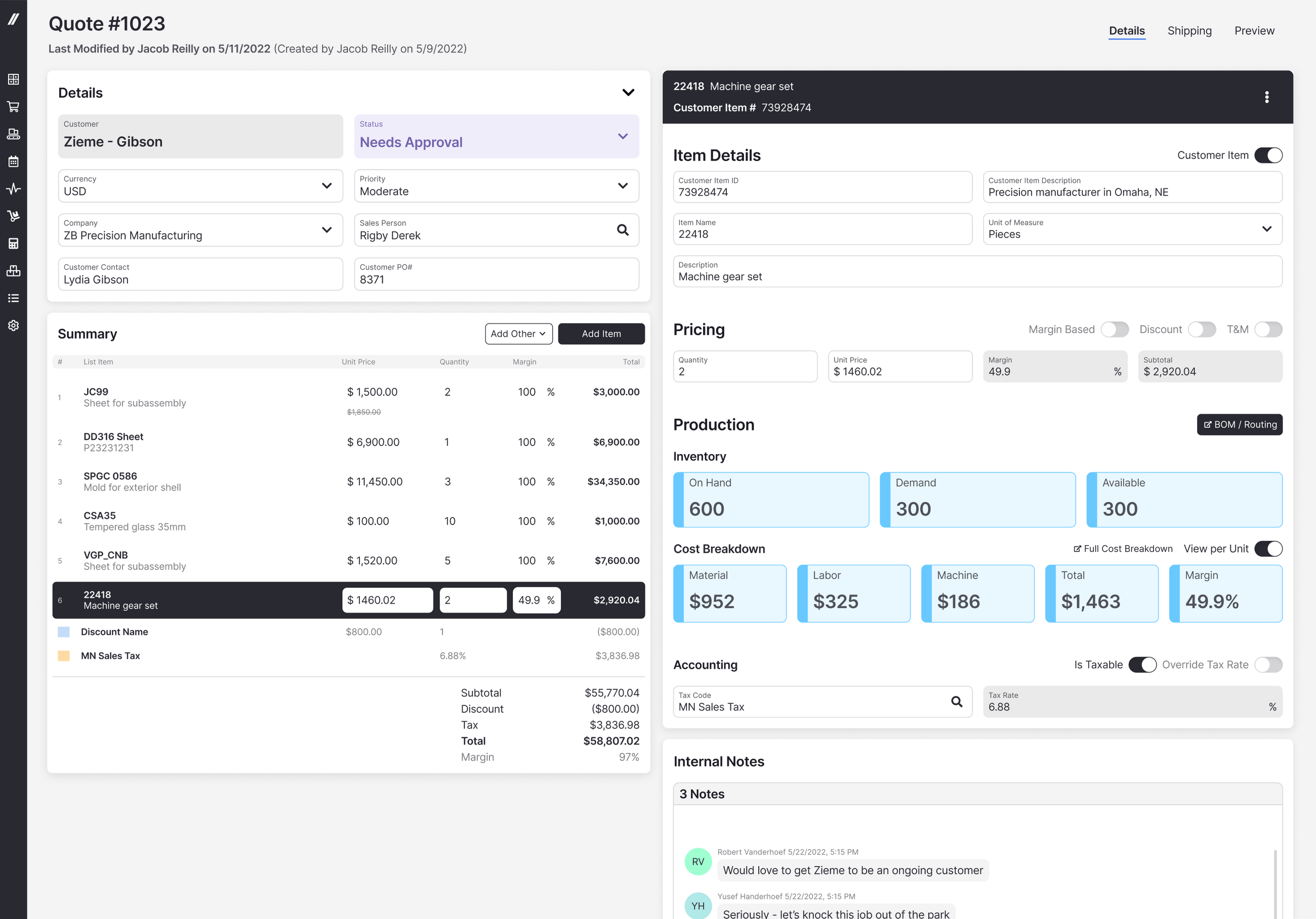
Purchasing Planning helps you plan and manage your purchasing activities based on current and future demand with automated purchasing recommendations. You can generate purchase orders automatically based on replenishment rules, minimum stock levels, lead times, and safety stock. You can also track purchase order status, receipts, invoices, and payments.
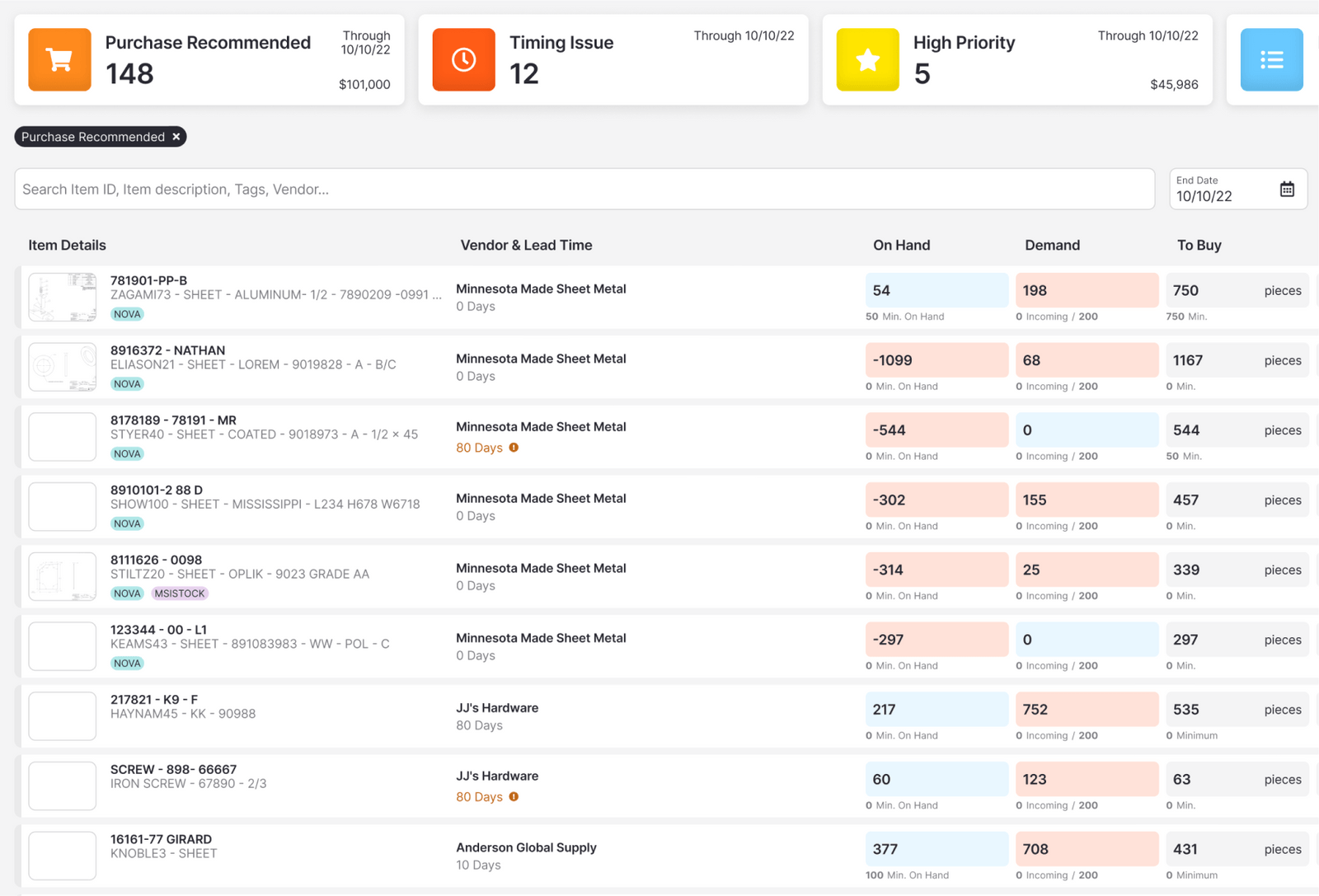
Demand Planning allows you to forecast and analyze demand patterns based on historical data, seasonality, trends, and other factors. You can create and compare multiple scenarios with actual demand to adjust your plans accordingly. You can also generate sales orders automatically based on forecasted demand or customer orders.
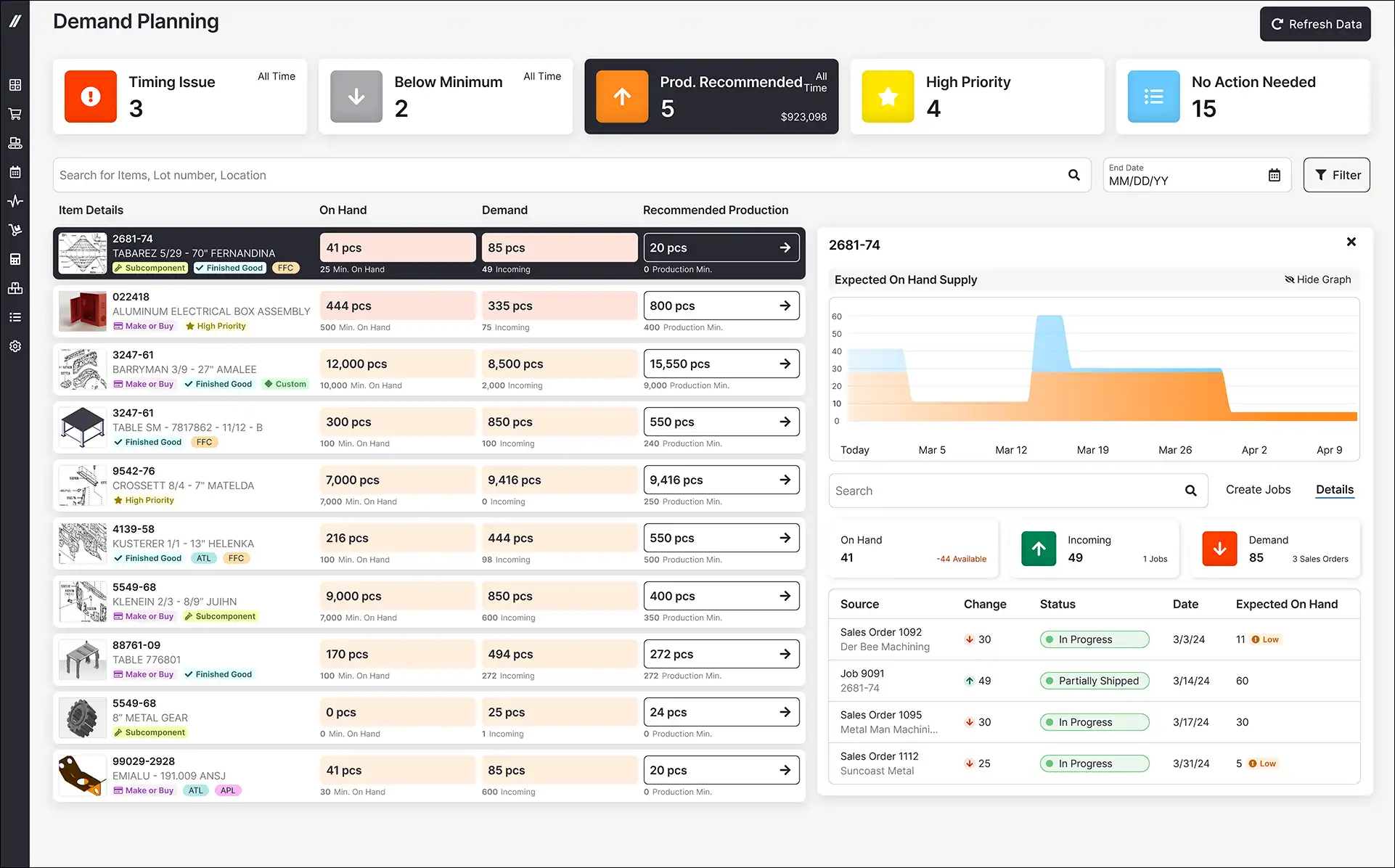
Production Scheduling gives you a schedule and optimizes activities based on available resources, capacity constraints, priority rules, and deadlines. You can assign work centers and machines, balance workloads, and monitor progress. You can also reschedule charges dynamically based on changing conditions and customer requests.
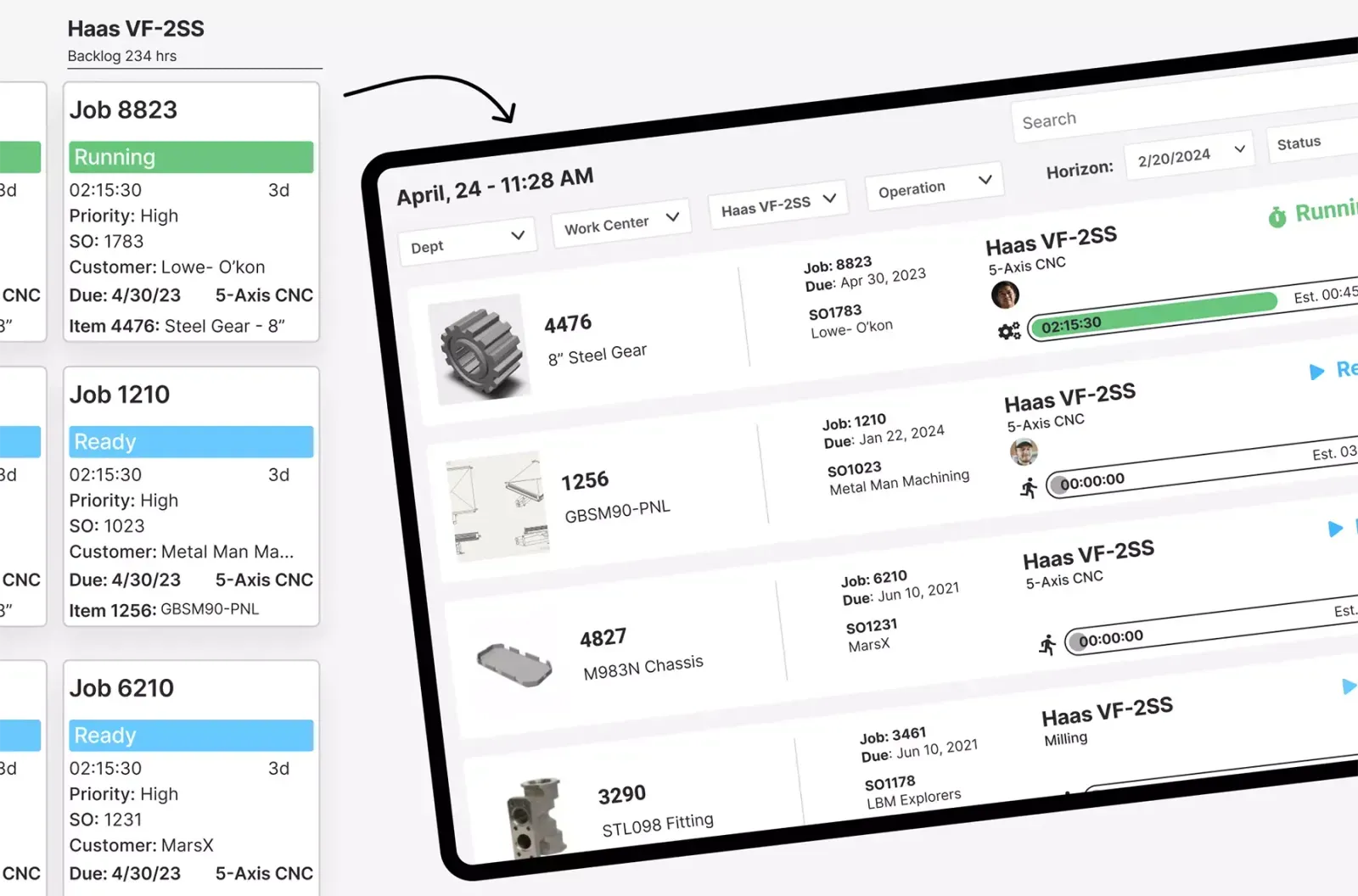
Job Tracking gives your shop floor everything they need to work on a job while tracking and managing your jobs from start to finish. In real-time, you can view job details, status, costs, and profitability. You can also record labor hours, material consumption, scrap and waste, quality checks and logs, and other job-related information.
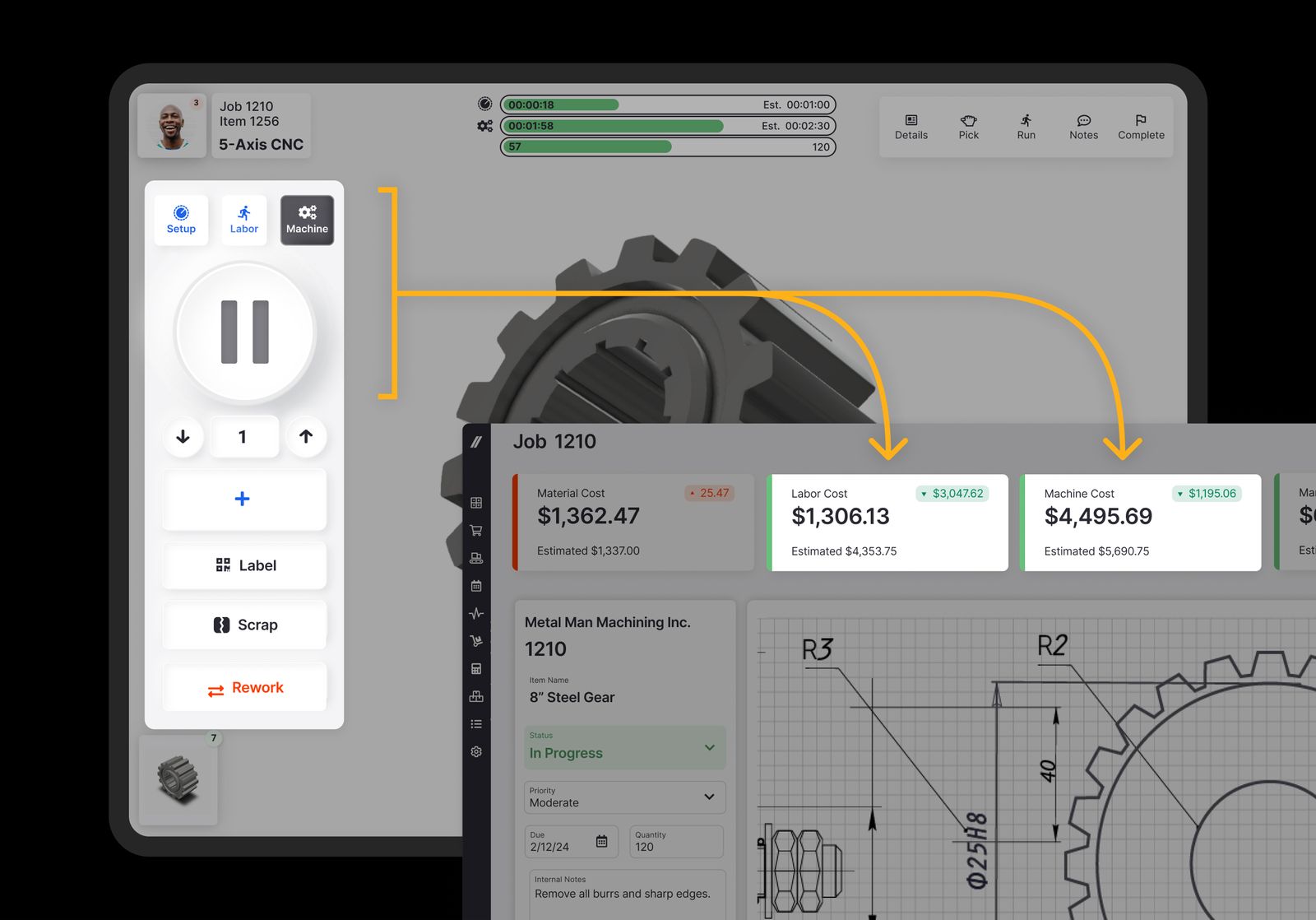
Production Tracking & Job Costing helps you measure and improve your production performance and profitability. You can collect and analyze live data from Job Tracking, automatically calculating actual costs versus estimated costs for each job — including labor, material, machine, and other expenses. You also can see live production progress, message the operators, edit or review the BOM & Routing, and create POs for needed materials.
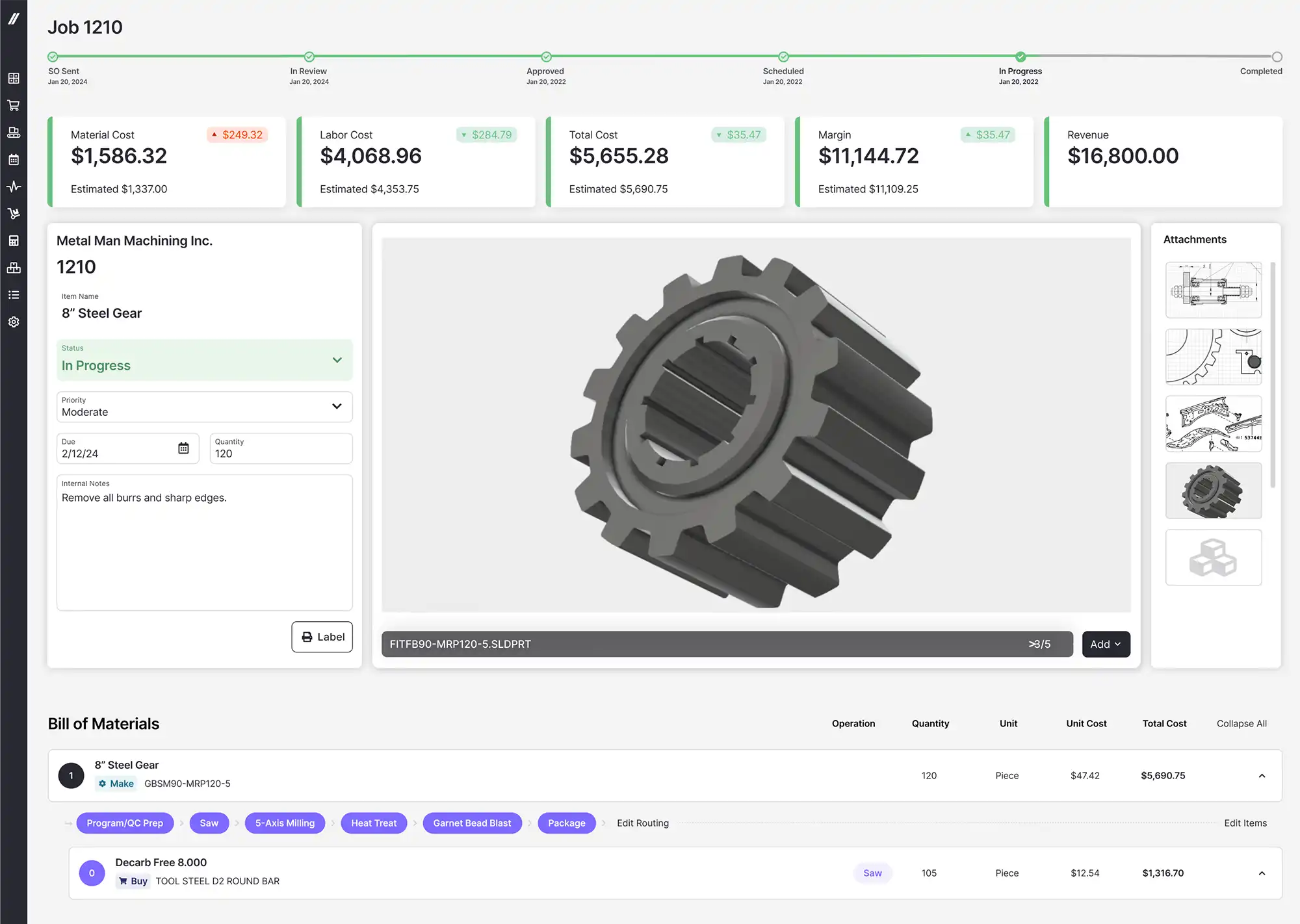
Quality Control helps you meet quality standards and compliance for your products and processes. You can define quality specifications and certifications for each item or process and perform quality inspections and tests at various stages of production. You can also record quality results, defects, non-conformances, and corrective actions. If you need to meet ISO9100 or AS9100 requirements, you should be able to generate quality reports and certificates for internal or external audits.
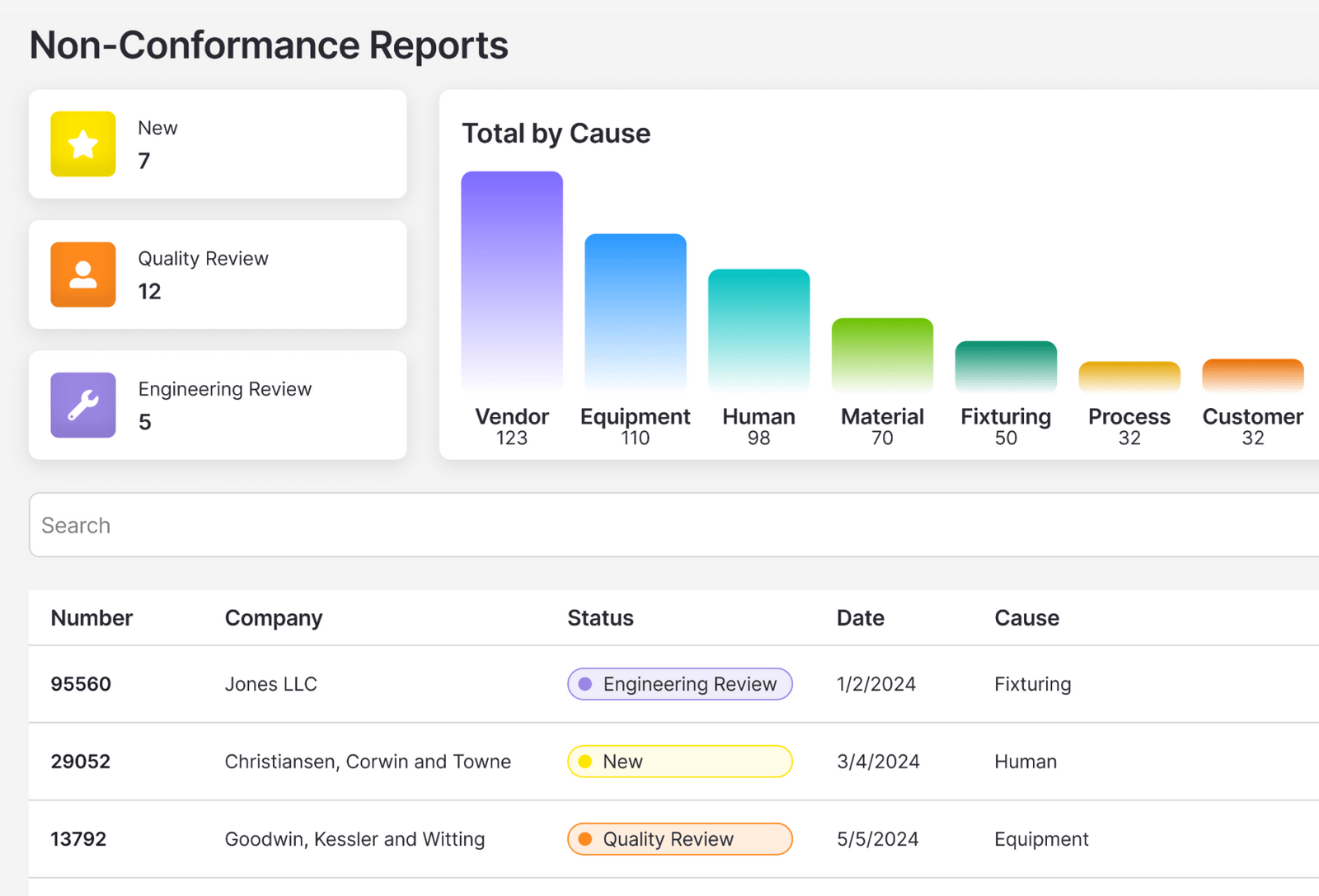
Inventory Management helps your team capture and manage your inventory levels and movements across multiple locations. You can track real-time inventory quantities, locations, lots, and expiration dates. Perform inventory transactions such as transfers, adjustments, issues, and returns, and conduct stock takes and reconcile inventory discrepancies.
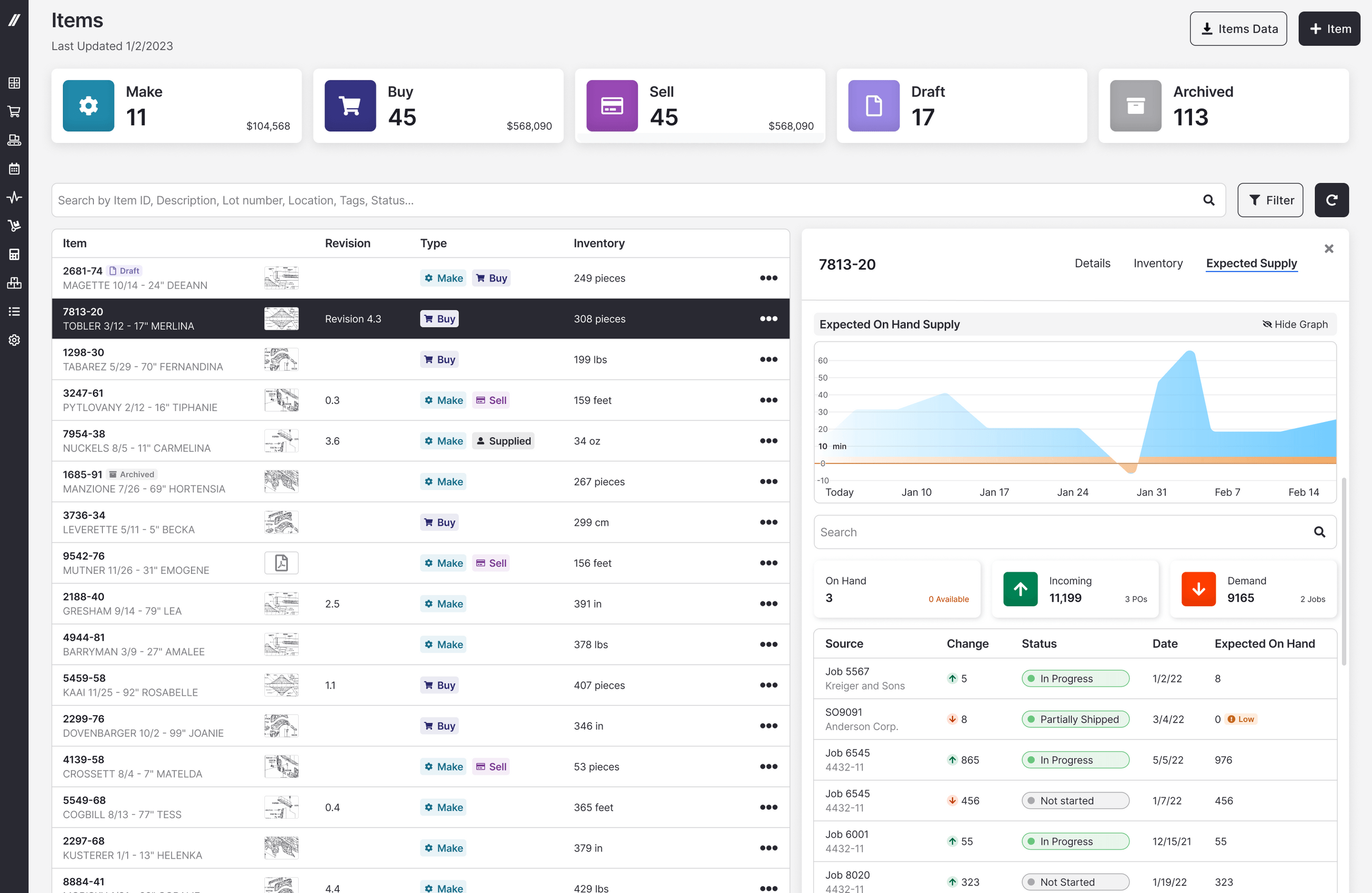
Shipping & Receiving helps you to create and print shipping documents, such as packing lists, labels, and bills of lading. You can also scan barcodes to verify items and quantities, update inventory and ERP records, and confirm shipments and deliveries. You can also handle returns and exchanges with ease.
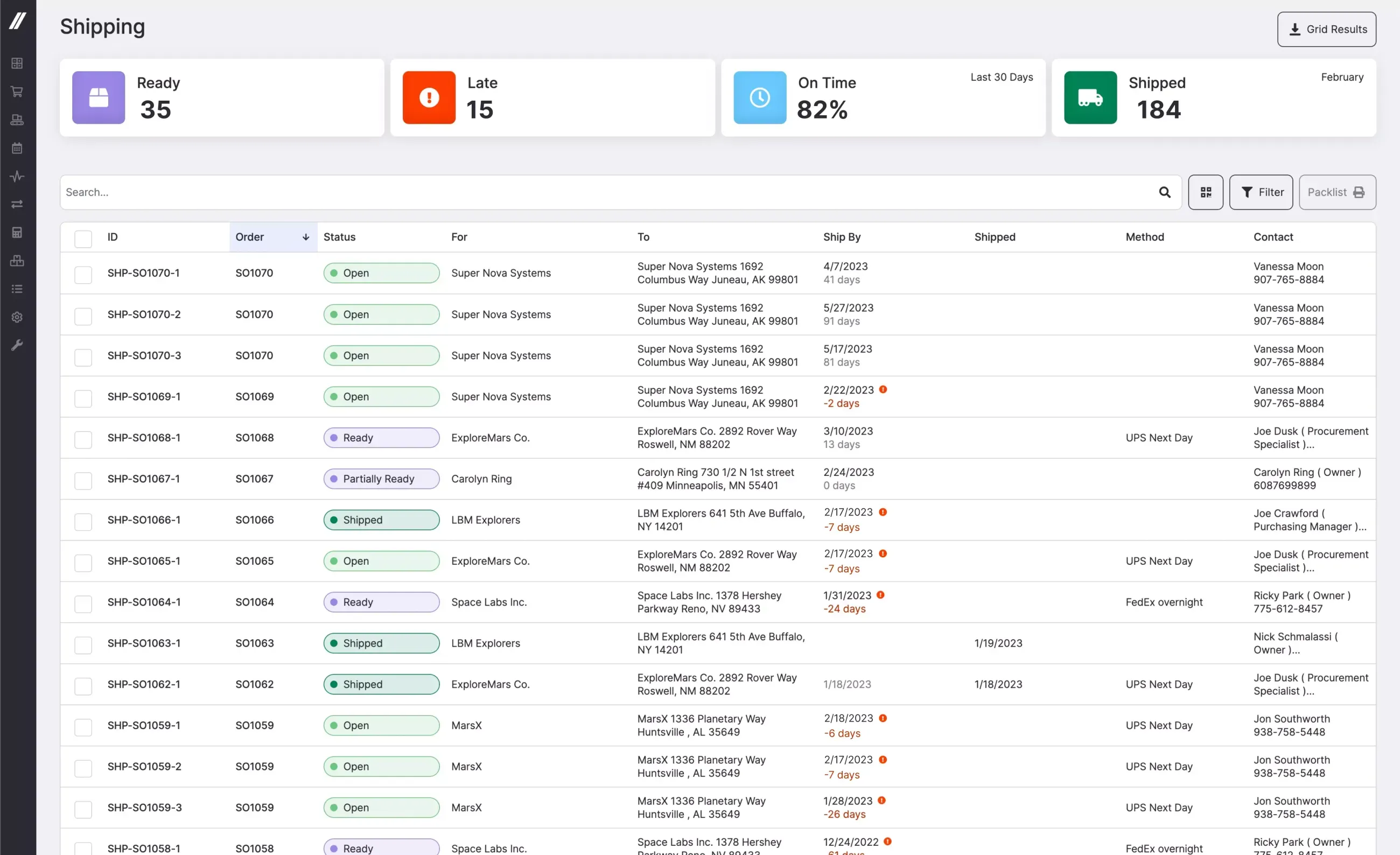
Reporting & Dashboards can provide valuable insights into your business performance and trends. Choose from predefined reports or create custom reports using various filters, parameters, and formats. You can also access dashboards that display key metrics and indicators in graphical or tabular form.
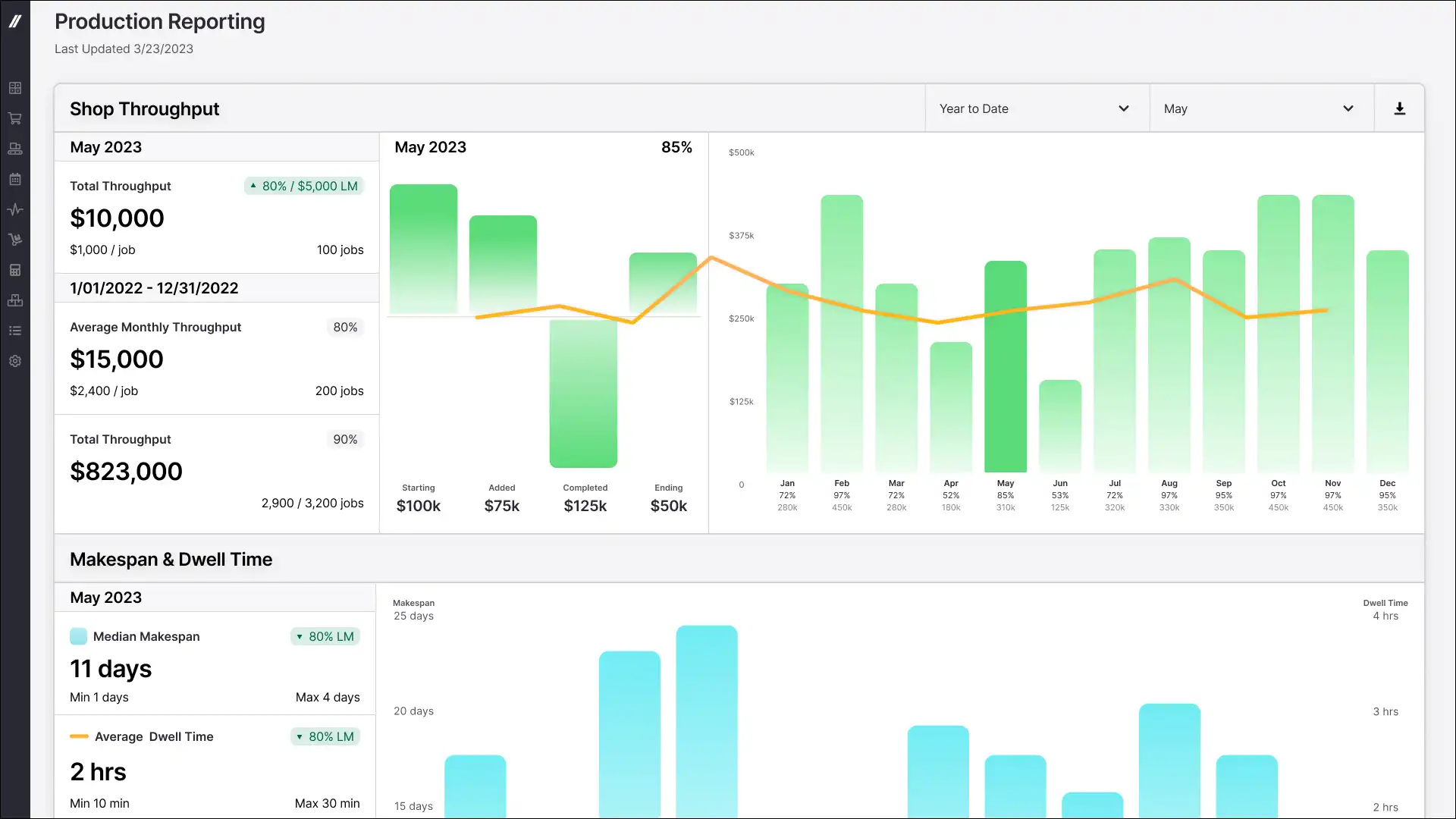
How to choose a metals ERP solution
Not all metals ERP solutions are created equal. You need to find a solution that meets your specific needs and goals. Here are some factors to consider when choosing a metals ERP solution:
- Industry expertise. Choose a solution that understands the nuances and complexities of the metal fabrication industry. You also need a vendor with experience working with businesses like yours that can provide best practices and guidance.
- Functionality. Find something that offers the features and capabilities relevant to your business processes. You may need a solution that integrates with your existing systems and tools, such as accounting or e-commerce software.
- Scalability. You need a solution that can grow with your business, support your future plans, and handle large volumes of data and transactions without compromising performance or security.
- Support. Pick a metals ERP with reliable implementation, technical support, and customer service — and provides regular updates and enhancements to keep up with industry trends and innovations.
Metals ERP software systems can help you streamline your processes, improve your performance, and increase your profitability in the metal fabrication industry. They can help you reduce costs, increase efficiency, enhance quality, improve customer service, and gain insights into your business. But remember, not all metals ERP solutions are the same. You need to find a solution designed for your needs today and your growth in the future.
If you are looking for a metals ERP solution to boost your metal fabrication business, consider Fulcrum. You can request a free demo or take a personalized product tour to see how Fulcrum can transform your operations and improve your bottom line.