Manufacturing ERP Implementation Failure: Pitfalls to Avoid
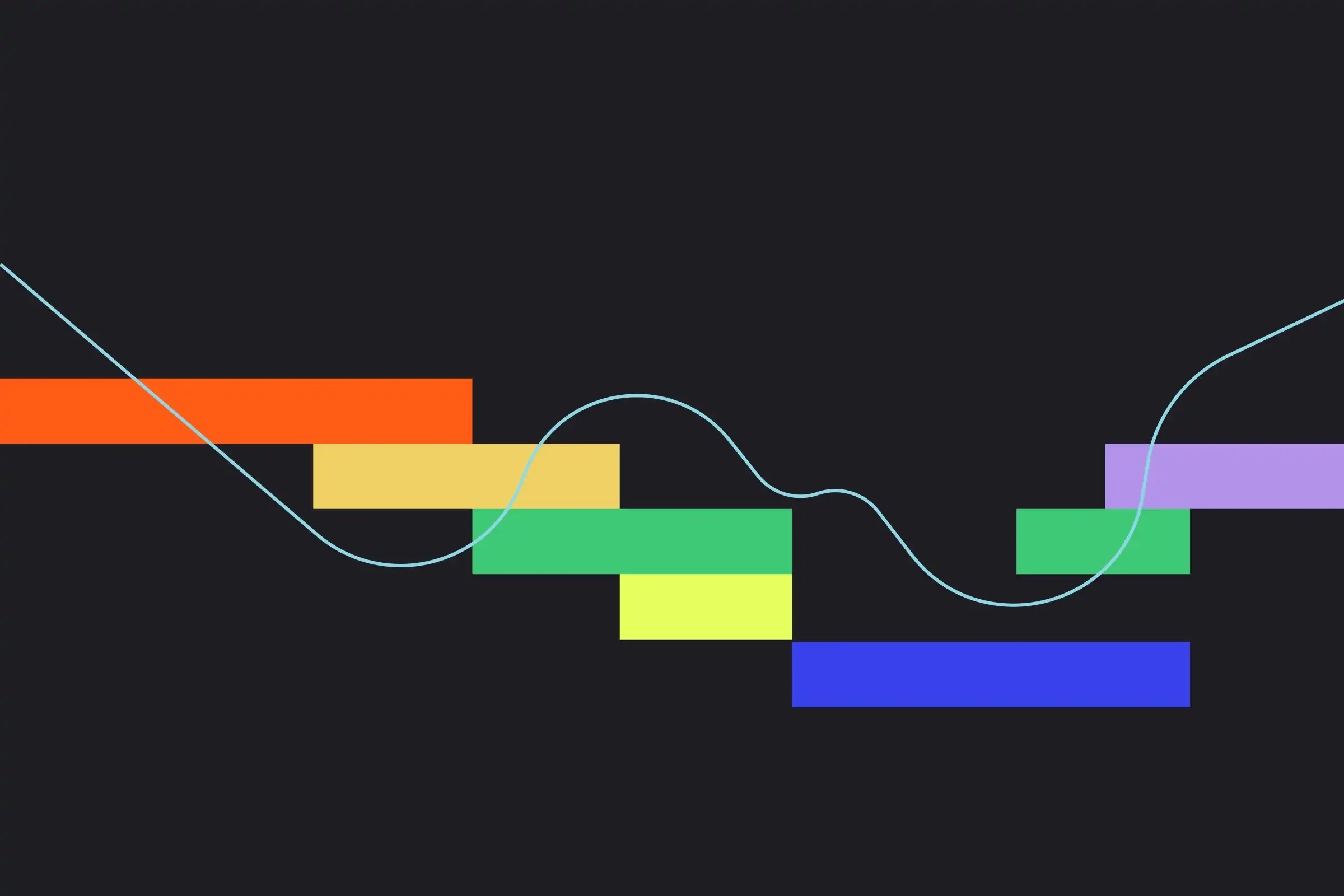
When you consider software to manage manufacturing — including sales, production, job tracking, fulfillment and accounting — an important area to get clarity on is the implementation for your ERP for manufacturing. A system that doesn’t start well usually ends up being a mismatch. But you can avoid or manage common potential pitfalls by being on the lookout for them. In working with our customers (and hearing past horror stories of ERP implementation failure), some challenges are most common:
ERP Implementation Timeline
Timing is often a big concern for shops looking to migrate their business to a new platform. No matter where you’re starting from, a manufacturing ERP implementation entails common steps: migrating data, coordinating a strategy for processes to work within the new system, and onboarding the entire team to the software. Many leadership teams see extended timelines as a liability for things to fall through the cracks as they jump between their existing software and the new platform. Having a timeline that’s established at the start of the implementation is key. But, more importantly, the ERP implementation timeline needs to be updated and communicated as frequently as it changes so that everyone is on the same page. One of the biggest causes of tension is an unclear timeline and proactively managing said timeline helps everyone ‘level-set’ their expectations for how the project is progressing.
ERP Data Migration
In today’s digital age, it would be a sight for sore eyes to see a manufacturing shop still tracking their processes only through pen and paper. Even if they utilize paper job travelers or diagrams, data is managed in some form of software application. For smaller companies this is usually a collection of excel spreadsheets, whereas larger shops will utilize a dedicated MRP/ERP system to manage their business. Regardless of method, implementing a new software requires that previous data be migrated to the new system. These sets of data include customers, vendors, current inventory counts and values, materials and their associated BOM/routing operations. Not all of this data is necessarily migrated, but a significant portion of it is.
Another additional consideration is the migration of historical data; will the team want to reference their old orders, materials, and contacts? Or are they looking to start fresh. Migrating data can be difficult if the legacy system pushes data in an awkward format. This aspect often requires significant work to transform the data into a format that can be put into the new system. Even the sheer volume of data can put stress on the customer as the implementation begins. Common questions at this stage revolve around whether the data will retain its integrity during migration, whether all the necessary data points are carried over from the legacy system, and if historical data can be pulled into the new system without cluttering the interface.
Feature Availability: Factors in Manufacturing ERP Implementation
There’s no such thing as a cookie cutter manufacturing shop. With all the different veins of manufacturing and specialized processes within those veins themselves. You’ll be hard pressed to find a shop running their business the same way as another, even if they fabricate similar materials. As a result, teams implementing a new software for their business will often have concerns about features that they feel are necessary to their process.
In situations where users want a feature that simply isn’t present or is still being built into the software, it’s important to communicate openly to relieve the tension that a feature gap creates.
Training (including for non-core team members)
Manufacturing ERP implementations typically start with a small team of leaders from the customer. Usually including any owners, production managers, and people from the finance side of things. As the implementation progresses this core team becomes familiar with the process of entering orders, creating jobs, purchasing, and whatever else they plan to use the software for. As the ‘go live’ date approaches however, a big question is how will the end users, i.e. those on the shop floor, sales team, and others who were not directly involved in the implementation will become acquainted with the software.
Training can look like a reference guide in the form of a Powerpoint or other document or a series of working sessions with the implementation. Another approach that can be effective depending on your culture is recording videos where the implementation team walks through the process that’s tailored to specific needs of each team. How the training is structured should be catered to the users and with the customer in mind. The person or team leading the project should outline routes for onboarding the team and establishing a timeline so that appropriate customer communication can be done when the time is right.
ERP Integrations with Other Software
Integrations are often the most tricky part of an implementation. From both a leadership and implementation team perspective, there are plenty of unknowns surrounding connecting software platforms that don’t automatically communicate. The biggest concerns are the frequency of data transfer and data integrity.
Data will need to be transferred between systems frequently enough that any new records are maintained in both systems. Integrity is important in that information about active customers and orders must be accurately maintained. A lack of data integrity introduces the potential for orders to be incorrectly outputted or materials incorrectly picked.
To get a firsthand view of how Fulcrum’s ERP implementation team differs from the rest, visit our Implementation page or schedule a demo.
// This article was update 4/04/23.